OSHA inspectors check if workplaces comply with the Occupational Safety and Health Administration (OSHA) regulations to ensure worker safety and prevent workplace-related incidents.
The Occupational Safety and Health Administration is a US federal government responsible for ensuring workplace safety. It’s the regulatory agency responsible for deploying certified inspectors to perform periodic inspections and investigate complaints regarding violations concerning workplace safety.
Table of Contents
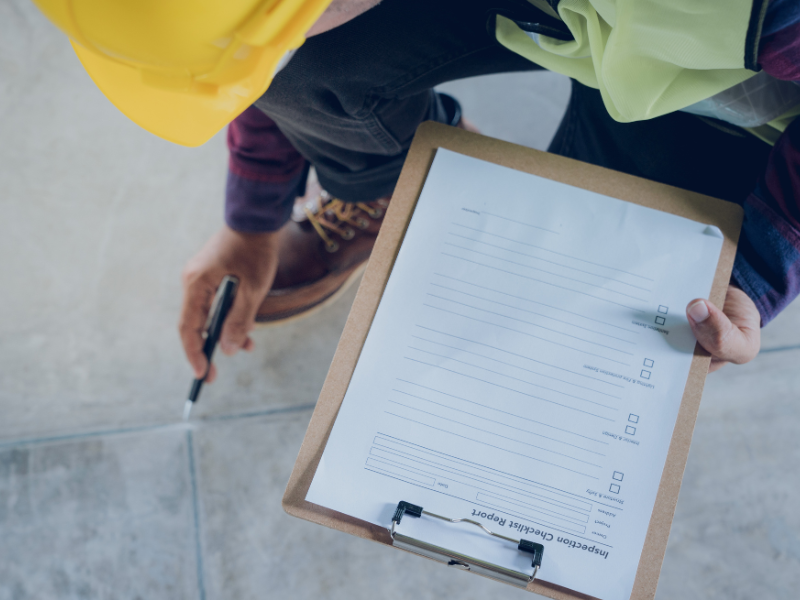
OSHA Inspectors: Qualifications and Training
Getting certified by OSHA to become an inspector requires a certain level of knowledge, expertise, and experience. Inspectors must also undergo a specialized training program and pass an examination demonstrating their capability to assess potential workplace hazards and evaluate security protocols.
OSHA inspectors can pursue any of the following specializations:
- Occupational health and safety: This involves assessing a workplace to check on factors contributing to employee safety and comfort, such as lightning, ventilation, and accommodations.
- Safety engineering: Inspectors check the design of the workplace and help companies comply with health and safety regulations.
- Industrial hygiene: Primarily involves addressing environmental concerns like noise, biohazards, and hazardous chemicals affecting employees’ well-being.
Education & training requirements
Depending on their specialization, inspectors must have at least a bachelor’s degree in occupational health and safety, industrial hygiene, occupational safety, environmental health, or a related field. Those who want to be an inspector but lack the minimum educational requirements must demonstrate sufficient work experience, attend OSHA training, and obtain OSHA certifications.
Familiarity with OSHA regulations and standards is essential. Inspectors need to understand federal and state occupational safety and health regulations and industry-specific standards.
Related experience
Relevant work experience in occupational safety and health is necessary. This could include experience in key areas such as workplace safety management, industrial hygiene, risk assessment, or regulatory compliance. Entry-level positions may require less experience, while senior roles may require several years of relevant experience.
They must also complete on-the-job training to learn inspection procedures, hazard recognition, and federal and safety regulations.
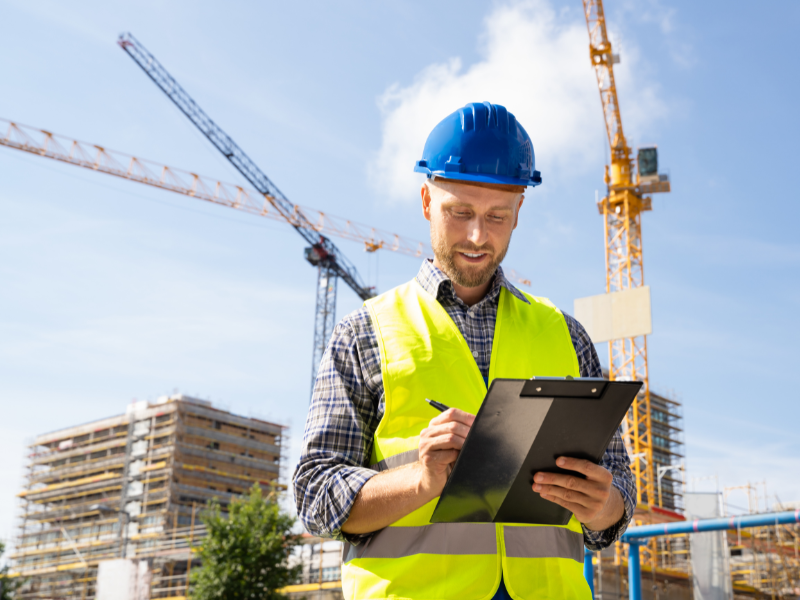
Soft Skills
Great attention to detail
Inspectors are required to spot even minor details that can become grave threats. To do this, they need to pay close attention to any details that can be potential safety and health hazards. The officers assigned to inspect must accurately document these findings in their inspection reports.
Problem-solving and analytical skills
Inspectors analyze workplace hazards and evaluate risks so they can recommend appropriate corrective actions to ensure compliance with safety regulations.
Strong communication skills
OSHA inspectors need strong communication skills to effectively explain citations and safety issues to people who may not be safety experts. They can be employers, employees, and other stakeholders present during inspections, investigations, and enforcement actions.
Inspectors must also be technically proficient in handling reports and know their way around a computer.
Willingness to travel
Inspectors don’t have the typical 9-5 office jobs. They must frequently visit offices, factories, hospitals, etc., to conduct inspections. They will also spend most of their working hours in the field and are often required to work more than 40 hours per week, even during odd hours.
Nice-to-Have Skills
It’s recommended (although optional) to earn OSHA certifications such as:
- Certified Occupational Safety Specialist (COSS)
- Environmental Master Certification
- Risk Management Master Certification
- Safety and Health Master Certification
- General Industry Certified Safety and Health Official
- Construction Certified Safety and Health Official
To qualify for leadership roles, it’s beneficial for OSHA inspectors to pursue advanced degrees.
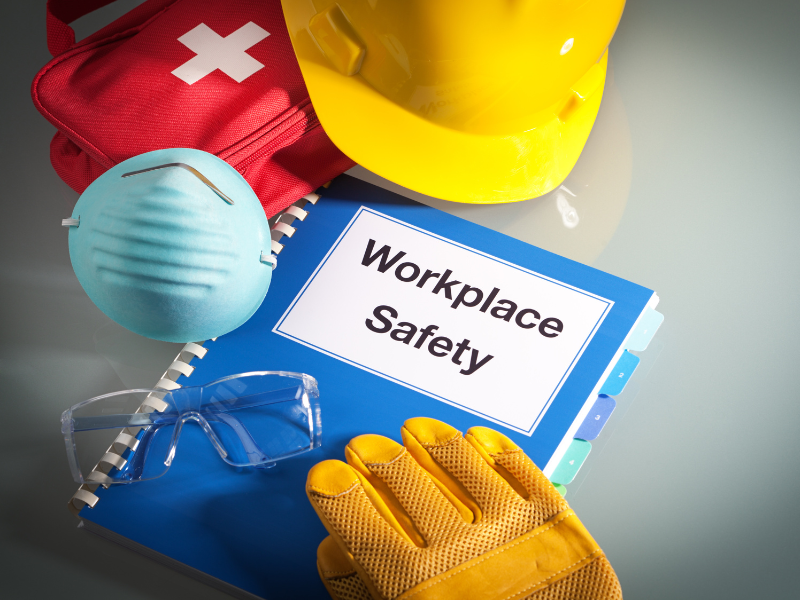
The Role of OSHA Inspectors
OSHA inspectors visit workplaces to assess compliance with safety and health regulations. They conduct routine inspections and respond to complaints or reports of workplace hazards. They also investigate workplace accidents and fatalities.
Some of their responsibilities include:
- Identify and evaluate workplace hazards like unsafe machinery, hazardous materials, electrical hazards, ergonomic risks, and unsafe working conditions.
- Enforce federal and state safety and health regulations by issuing citations, fines, and penalties for violations.
- Provide guidance and educational resources to employers and employees on safety and health practices, regulations, and standards
- Investigate workplace accidents, injuries, illnesses, and fatalities to determine their causes and whether any safety violations occurred.
- Respond to complaints from workers, unions, or other sources regarding unsafe working conditions.
- Prepare reports detailing observed hazards, violations of regulations, corrective actions required, and any citations or penalties issued.
- Conduct follow-up visits to ensure employers have corrected identified hazards and complied with OSHA regulations.
- Monitor ongoing compliance with safety and health standards to prevent recurring violations.
- Maintain accurate records of inspections, investigations, citations, penalties, and other enforcement activities.
Interacting With OSHA Inspectors
Whether it’s a surprise or a planned visit, you should cooperate fully with OSHA inspectors. To verify their identity, you can respectfully request proper authorization.
Once they’ve identified themselves, escort them throughout the facility and answer all questions truthfully. Also, it’s best to encourage employees to cooperate and answer any queries.
By being professional and accommodating, you can avoid unnecessary inspection delays. This proactive approach also shows your willingness to foster a positive relationship with OSHA.